Lime Slaking Systems
Lime Slaking Systems
At Carmeuse Systems, we understand the vital role lime slaking system design has in producing an effective lime slurry and how the quality of your slaked lime can have a major impact on downstream processes, chemical composition, material cost, and your overall operating costs. When developing a custom lime slaking system, the first step is selecting the right type of slaker based on your parameters, such as pebble size and water composition. Our teams collaborate with you to determine the best option for your process and budget, offering detention, batch type / mix tanks, vertical ball mill, and portable lime slakers.
The slaker, however, is just one component of a comprehensive lime slaking system. Our engineering teams are experts in developing complete solutions, encompassing dry material storage, flow promotion, conveying, slaking, and slurry storage, depending on your specific needs and available footprint. Whether you are looking for a new lime slaking system, to retrofit an existing system, or to improve the effectiveness of your current lime slaking operations, Carmeuse Systems is ready to assist.
Features&Benefits
Features & Benefits
Carmeuse Systems’ custom lime slaking systems are designed to optimize the slaking process, with high-quality lime slurry production tailored to your operational needs.
- Customization: Carmeuse Systems collaborates with you to design a slaking system that meets your unique requirements, considering factors like lime quality, water temperature, and consumption rates. This includes various types of slakers, including detention, batch type, and vertical ball mill slakers, each suited to different applications and lime qualities.
- Efficiency: Our lime slaking systems are engineered to maximize lime usage efficiency, reducing overall lime consumption and operational costs.
- Safety and Reliability: The systems are designed with safety and reliability in mind, minimizing the risk of operational downtime and ensuring consistent performance.
Capabilities
CAPABILITIES
Carmeuse Systems has over 50+ years of experience developing lime slaking systems. Whether you are looking for a new lime slaking system or to enhance or retrofit an existing system, Carmeuse Systems can accommodate your needs.
Understanding Your Supply
In addition to providing technical expertise on lime slaking equipment, Carmeuse Systems is also backed by a global leader in lime and limestone supply, Carmeuse. Together, our teams have an in-depth understanding of the complexities of lime and can provide our customers unrivaled guidance for their lime handling application.
Choosing the Right Slaker
We design and provide a variety of slaker types, but first, we collaborate with you to determine the best option for your process and budget. Carmeuse Systems takes the time to understand your application, process and site-specific needs, ensuring you get the right type of lime slaker optimized for your operation.
Ongoing System Support
During startup, we will be onsite to ensure everything goes as planned, answer any questions, and make necessary adjustments. After startup, Carmeuse Systems will continue to be there offering maintenance support, systems reviews, system optimization studies, operator training, troubleshooting and spare parts.
Specifications
Specifications
Our lime slaking systems are available in a range of sizes and configurations to meet the diverse needs of our clients and can be customized to suit your site’s specifications. To discuss your specific needs, we suggest contacting us to speak with our engineering team.
Here are some general specifications:
- Silos/Storage: Available in various capacities, from small-scale storage bins and hoppers to large silos; we can help you determine what makes sense for your process.
- Dust Control: Our experts can ensure your customized system has a dust control process that creates a clean and safe workspace.
- Feed & Conveying Systems: Equipped with advanced feed systems for precise and consistent chemical dosing and conveying systems.
- Slakers: With a range of available slaker types and sizes, Carmeuse Systems will work with you to understand your production needs to recommend an appropriate slaker.
- Slurry Storage & Pumping: It is critical to keep lime slurry in suspension when storing. Carmeuse Systems can provide effective slurry storage and pumping solutions so that your slurry can be effectively transferred to your downstream application when needed.
Our lime slaking systems are designed to provide reliable and efficient performance, ensuring safe and effective slurry production. Contact us today to learn more about how our solutions can benefit your operation.
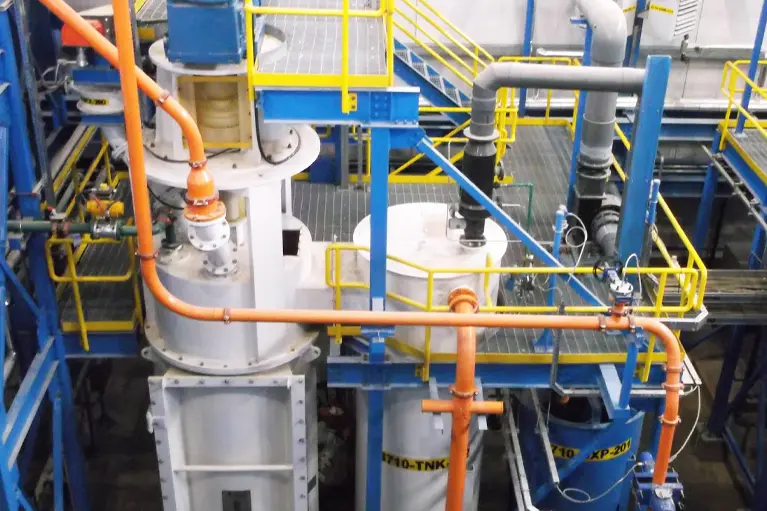
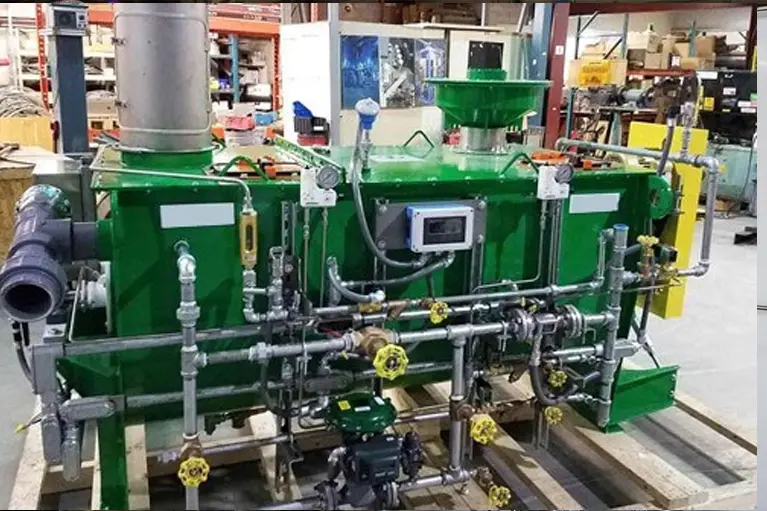
End-2-End Support
When it comes to lime slaking systems, Carmeuse Systems is your go-to solution provider from End-2-End. As part of Carmeuse, we understand the systems necessary to handle lime slaking effectively but also the intricacies of the raw material itself. Carmeuse is a leading provider of lime and limestone products and through our End-2-End Services, we support customers from the mines where the raw material is produced through to the point of application.
The benefits of working with Carmeuse Systems includes:
- Expertise in Lime and Limestone
- Engineering and Design Expertise for Complete Lime Handling Systems
- Component Parts to Integrate into Existing Applications
- System Retrofits and Upgrades
- Maintenance and Replacement Parts at the Ready
- Access to Experts to Diagnose System Issues and Improve Efficiencies
- Laboratory Services through our Innovation Center
Learn more about our End-2-End Services.