Systems
Bulk Material Handling Systems
Any process requiring a dry bulk material needs a material handling system designed to get it from the point of receipt to the point of use. This will include various combinations of conveyors, silos, bins, chutes and flow promotion devices. Carmeuse Systems will help you select the right bulk material handling equipment to suit the specifics of the material you are handling, and the unique challenges to your facility.
Our Bulk Material Handling Solutions are designed to efficiently handle and store dry bulk reagents such as lime, soda ash, magnesium oxide, and others. We understand the importance of an effective bulk material handling processes for your application. We also recognize that every bulk material handling situation is unique and extensive expertise is required to build a customized system to meet your specifications and footprint requirements.
At Carmeuse Systems, we have the knowledge and engineering expertise to build a bulk handling system customized to your needs effectively. We understand that these systems are crucial for various industrial applications to ensure safe, reliable, and cost-effective storage and feeding of bulk material into your process. Whether you are in water treatment, mining, or any other industry requiring bulk chemical handling, our solutions are tailored to meet your specific needs.
Our bulk chemical storage systems are engineered to provide optimal performance and longevity. They are built with high-quality materials to withstand harsh environmental conditions and ensure the integrity of the storage, conveying, and handling of your reagent. With our bulk handling systems, you can achieve seamless integration into your existing processes, enhancing operational efficiency and safety.
Interested in a custom dry bulk material handling system or have the need for a pre-engineered system? Please contact us.
What Equipment is Considered When Building a Bulk Handling System?
A dry bulk material handling system includes equipment like:
- Pneumatic conveying systems
- Blowers
- Screw conveyors
- Belt or chain conveyors
- Bucket elevators
- Air slides
- Automation and Controls
In addition to the products listed above, bulk chemical storage solutions are also necessary, including:
- Silos
- Bins
- Hoppers
- Dust collection systems
Carmeuse Systems works with you to design the optimal combination of bulk material handling equipment based on your specific needs. Our goal is to select the right combination of equipment for you to receive material from either truck, rail or bulk bag, and transfer the material seamlessly into your application.
Features&Benefits
Features & Benefits of Bulk Material Handling Systems
Carmeuse Systems’ custom bulk chemical storage and feed systems are tailored to your operational needs.
- Customization: Carmeuse Systems collaborates with you to design a storage and feed system that meets your unique requirements for bulk material handling, providing flexibility and adaptability.
- Expert Engineering: Our engineering experts have a deep understanding of the necessary system components and the raw material being handled, to ensure efficient dry bulk material handling system design and operation.
- High Quality Construction: Our bulk handling systems are built with quality materials to ensure durability, long-term performance, and reduce maintenance costs.
- Efficiency: Our feed systems are engineered to provide precise and consistent chemical dosing, improving process control.
- Easy Installation and Integration: At Carmeuse Systems, we simplify the setup process, minimizing downtime and disruption for your operation.
Benefits of Well-Designed Bulk Material Handling Equipment
When Carmeuse Systems designs bulk material handling equipment our goal is to make sure the material arrives reliably and safely at the destination to ensure uninterrupted operation at your facility. With many bulk materials we must also ensure that the solution provided focuses on maintaining product integrity, so the material is delivered to process in the same condition as it arrived on site.
Carmeuse Systems has been designing bulk material handling systems to handle bulk material products both mechanically and pneumatically for over 50 years. This experience provides us with the engineering expertise to design the best process and supply the appropriate equipment to ensure your operations run safely and efficiently. We consider all the site-specific factors and variables to provide you with the best solution to address your plant’s specific needs. What makes Carmeuse Systems different is our diverse experience in many applications, industries, and chemicals, along with the ability to support your system from concept through to decommissioning, and everything in between.
Benefits of Working with Carmeuse Systems When Designing Your System
There are many different bulk material handling system manufacturers. It is important that the company that you work with understands the needs of your specific application including the raw material being handled. Carmeuse Systems is owned by Carmeuse, one of the most well-known and well-respected lime and limestone manufacturers in the world. Our experts understand the raw materials that go into the bulk material handling system you are using and are therefore better equipped to understand the type of components that will be best suited to your needs.
Working with a company that understands not only the system design and engineering, but also the raw material going through the system ensures that your system is built efficiently and will provide peace of mind that your bulk material handling system is working at maximum effectiveness. In addition to our engineering and raw material expertise, Carmeuse Systems also provides End-2-End Services to our customers, which provides additional support far past design and commissioning and ensures that we serve as an expert partner throughout the lifetime of the bulk material handling system.
Capabilities
Capabilities and Our Expertise in Bulk Material Handling Equipment
Our teams have decades of combined experience in building dry bulk reagent handling systems where all components work together effectively. We are truly a partner in this critical component of your application, and we have knowledge in every aspect of this system from truck offloading and conveying systems through to storage of various dry bulk reagents. Whether you have a system that needs replacement of repair, or if you are in need of an entirely new system, trust your project to the experts.
Specifications
Specifications
Our dry bulk material handling equipment solutions are available in a range of sizes and configurations to meet the diverse needs of our clients and can be customized to suit your sites specifications. To discuss your specific bulk material handling needs, we suggest contacting us to speak with our engineering team.
Here are some general specifications:
- Silos/Storage: Available in various capacities, from small-scale storage bins and hoppers to large silos; we can help you determine what makes sense for your process.
- Dust Control: Bulk chemical storage requires the use of dust control measures to prevent unsafe and wasteful working environments. Our experts can ensure your customized system has a dust control process that creates a clean and safe workspace.
- Feed & Conveying Systems: Equipped with advanced feed systems for precise and consistent chemical dosing and conveying systems that suit your reagent included pneumatic conveying, screw conveying, belt conveying, and more.
- Automations & Controls: Metering and control systems are available that are specific to the customized system that has been created for your site. With the ability to monitor the operation of your system, you will have peace of mind.
- Reagents Utilized: Suitable for storing and handling a wide range of bulk reagents, including lime, soda ash, alum, magnesium oxide, and more.
Our bulk handling systems are designed to provide reliable and efficient performance, ensuring the safe and effective handling of your bulk chemicals. Contact us today to learn more about how our solutions can benefit your operation.
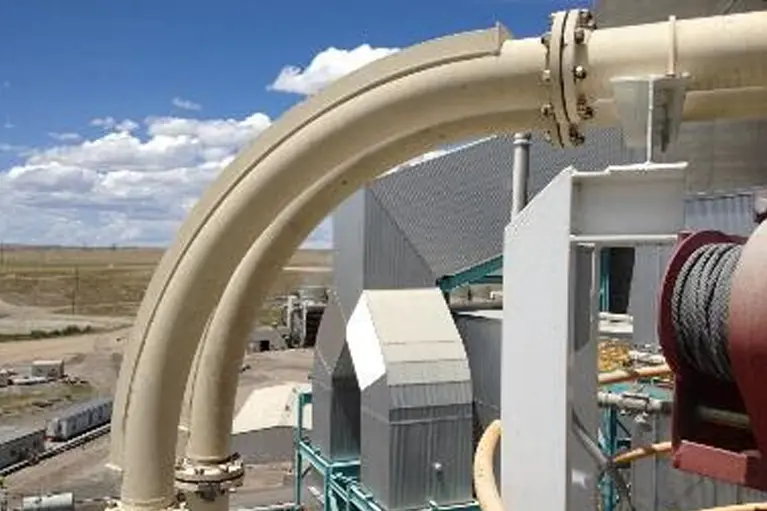
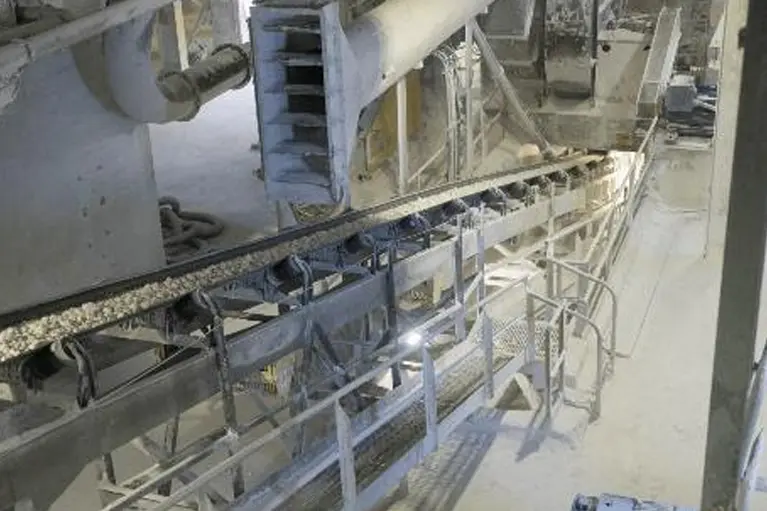
End-2-End Support for Bulk Material Handling Equipment
When it comes to engineering a lime or dry bulk material handling system, Carmeuse Systems is your go-to solution provider from End-2-End. By utilizing the experts at Carmeuse Systems, you ensure that all of the aspects of your dry bulk material handling equipment works seamlessly together, reducing the risk of issues and ensuring that your system functions smoothly.
As part of Carmeuse, we understand the systems necessary to handle dry materials effectively but also the intricacies of the raw material itself. Carmeuse is a leading provider of lime and limestone products and through our End-2-End Services, we support customers from the mines where the raw material is produced through to the point of application.
The benefits of working with Carmeuse Systems includes:
- Expertise in Lime and Limestone
- Engineering and Design Expertise for Dry Bulk Handling Systems
- Component Parts to Integrate into Existing Applications
- System Retrofits and Upgrades
- Maintenance and Replacement Parts at the Ready
- Access to Experts to Diagnose System Issues and Improve Efficiencies
- Laboratory Services through our Innovation Center
Learn more about our End-2-End Services.
Two Factors that Influence Design
Understanding the characteristics of the material that you are handling and processing is essential when selecting your bulk material handling equipment. Several key considerations need to be considered when designing your handling systems:
- What is the bulk density?
- Compressibility - does the bulk density change?
- What is the particle size distribution?
- What is the material shape (powder, grain, crystal, prill, flake, granule, lump)?
- Is the material friable? Does the size matter to process?
- What is the angle of repose?
- What is the flowability? Will it bridge, rat hole?
- Will it compact with vibration or on its own over time?
- Will the material flood?
- Hygroscopic - will it absorb moisture?
- Is the material perishable?
- Is the material compatible for corrosion?
- Is it an agglomerated material?
- Is it sensitive to contamination, water?
- Is it explosive? Toxic? Abrasive? Heat sensitive?
Knowing these material characteristics influences how we design a system using the right bulk material handling equipment to successfully convey and process your bulk materials.
Understanding the process by which the bulk material goes through once it arrives at your site is critical when designing and selecting your bulk material handling equipment. Several key considerations need to be considered:
- How is the product delivered (truck, rail, container, bulk bag)?
- How is the product unloaded (pneumatic, dump truck)?
- Where will it be stored (silo, day bin, warehouse)?
- How long will the product be kept in storage (days, weeks, months)?
- What will the material consumption rate be?
- Will it be fed to process dry, or will it need to be wet or slaked?
- Are there any site-specific challenges, climate, terrain obstacles that need to be avoided?
When all of these points are considered, our team at Carmeuse Systems can help guide you in selecting and designing the right bulk material handling system that will work best for your specific application.
FAQs
Bulk material handling equipment is the collective term for the machinery used to move dry products from one place to another. This can be done either mechanically using conveyors (screws, belts, buckets etc.) or pneumatically using convey air (pressure or vacuum).
Mechanical convey tools consist principally of screw conveyors, belt conveyors, chain conveyors, and bucket elevators. Pneumatic conveyors use blowers to suspend product in air and move material through pipe.
The three principle requirements for material handling are (1) ensuring material is moved from origin to destination at the rate necessary, (2) without losing product and (3) minimizing degradation.
In broad terms there are two main techniques for material handling: mechanical conveying where material is physically pushed or pulled using a conveyor such as a screw or bucket and pneumatic conveying where material is conveyed using air in pressure or vacuum to suspend the product.