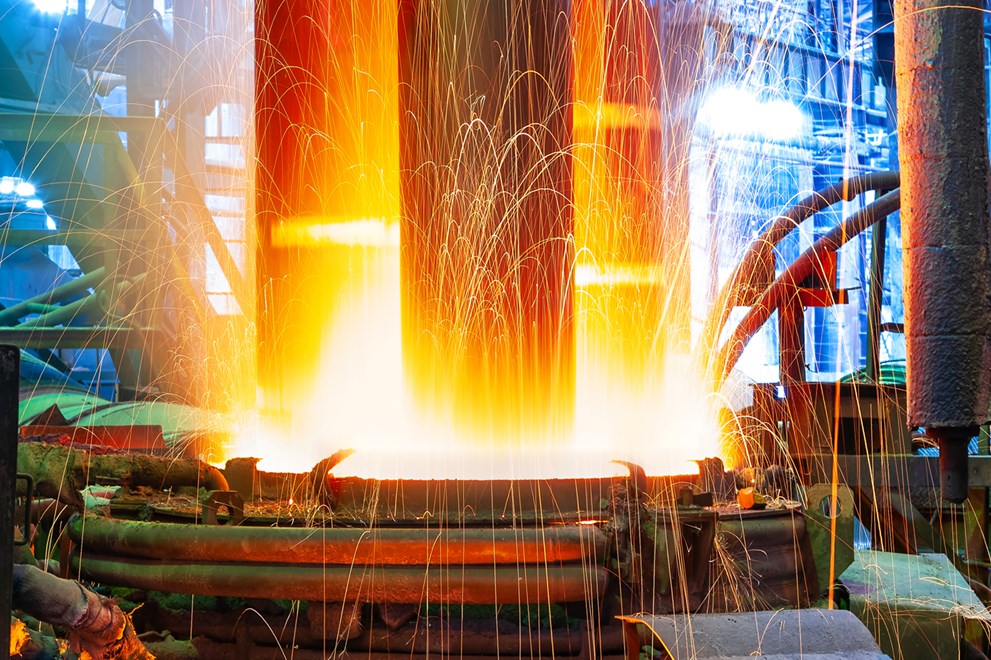
The Lime Injection Journey
A Better Way to Add Lime
Historically, steelmakers have experimented with various methods for adding lime to the EAF. Some of the lime addition technologies still in use include scrap bucket discharge, 5th hole addition through the roof, super sack drops, and briquetting metallurgical lime screenings. One drawback for the traditional methods was their tendency to create environmental concerns in the shop due to rogue lime emissions. Utilizing the 5th hole through the roof was developed to help reduce dust loss but did not resolve lime fines being generated through the various drop points during its conveyance. Ultimately, whether lost to the shop environment or baghouse, the result is the same - reduced lime yield. Another drawback to these methods developed with the emergence of the foamy slag practice. For this process, it is highly desirable that lime be added to the process at the right time and in the right position within the furnace to protect the furnace sidewall and refractory.
These shortcomings ushered in the first attempts at sidewall lime injection in the early 1990s. Since then, advances have been made in areas of equipment design, slag practice and lime quality. Today, lime injection provides a reliable technology for steelmakers to control foamy slag, reduce waste disposal, improve safety and save electrical energy. Implementing lime injection technologies can lead to cost savings by reducing waste, enhancing energy efficiency, and extending the lifespan of EAF refractories.
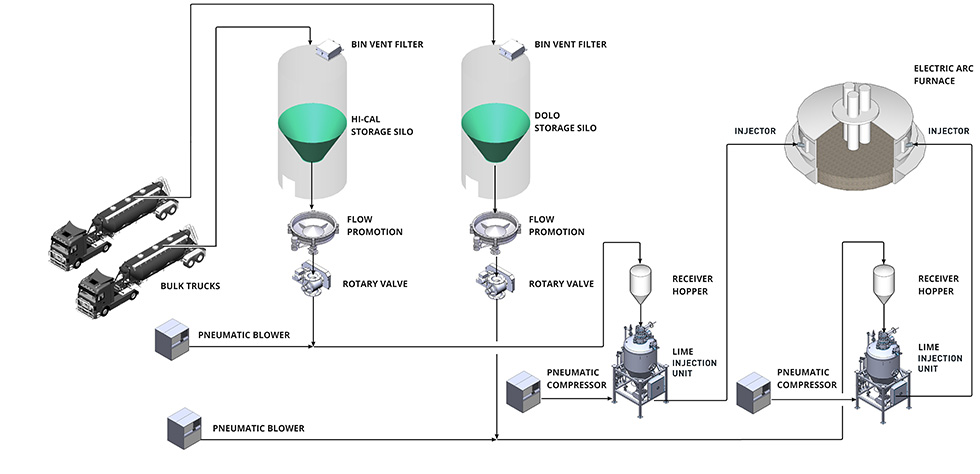
Reducing Lime Waste
Lime and dolime are essential in steelmaking, but traditional methods of lime addition, such as via scrap buckets or fifth-hole addition, are prone to inefficiencies and waste. Lime injection establishes a closed-loop system, using pneumatic conveying to transport lime and dolime from storage areas to the EAF. This closed loop reduces lime loss/waste at transfer points, minimizes dust accumulations around the shop, and results in a cleaner working environment. Lime injection technologies also improve dosing accuracy by delivering lime and dolime directly into the furnace via sidewall injectors. By injecting material at supersonic speeds into the bath, it ensures that more lime is used in solution and further reduces material loss to the baghouse. The precise control afforded by injection allows the exact amount of lime needed to be added at the right time in the heat. More precision helps improve system efficiency and prevents unnecessary overuse of lime. Together, this can lead to a 7-15% reduction in lime consumption and material cost savings.
Enhancing Energy Efficiency
There is an extensive history on lime’s use as a fluxing agent in steelmaking. Through the development of viable injection technologies, the benefits that lime provides in the steel-making process are better realized. Injection of high calcium lime and dolomitic lime throughout the melting process, rather than supplemental additions late in the heat, leads to improved slag chemistry and energy savings as it allows for the direct delivery of smaller sized hi cal and dolime into the bath, reducing the energy required to melt the material into solution.
The evolution of foamy slag practices and the benefit it provides to making cleaner steel has been key to the further development and optimization of lime injection. Cleaner steel is not the only result of foamy slag practices. Additional benefits include: reduced electrical demand, improved arc stability, reduced noise, improved productivity, lower nitrogen levels, satisfied MgO solubility, improved basicity control, and increased refractory life in the furnace.
Extending the Lifespan of the Refractory
The pneumatic injection of quicklime and dolime in electric arc furnaces (EAF) is a well-proven improvement versus the practice of charging fluxes by conveyor belt systems and 5th hole roof opening. It improves refractory protection, continuous slag foaming, viscosity control, distribution in the bath surface and overall process optimization. By use of fluxes fine particles, the system allows a reactive and faster solution all while reducing dust generation from the conveyors system.
The magnesium content in dolomitic quicklime plays a crucial role in preventing melt-throughs in the refractory, thereby extending the lifespan of the furnace. The efficient use of lime and dolime through this injection process can help extend the lifespan of refractory linings and electrodes. Over time, the efficiencies gained from lime injection can reduce consumable expenses, leading to a significant impact on costs.
Choosing Lime Injection
In recent years, the popularity of lime injection has grown. With the benefits becoming more well-known, for many the question is fast becoming not whether to implement lime injection, but how to do so in the most effective way. For guidance on implementing lime injection, or for an evaluation of your current lime injection systems, contact our team at Carmeuse Systems.
Related Blogs
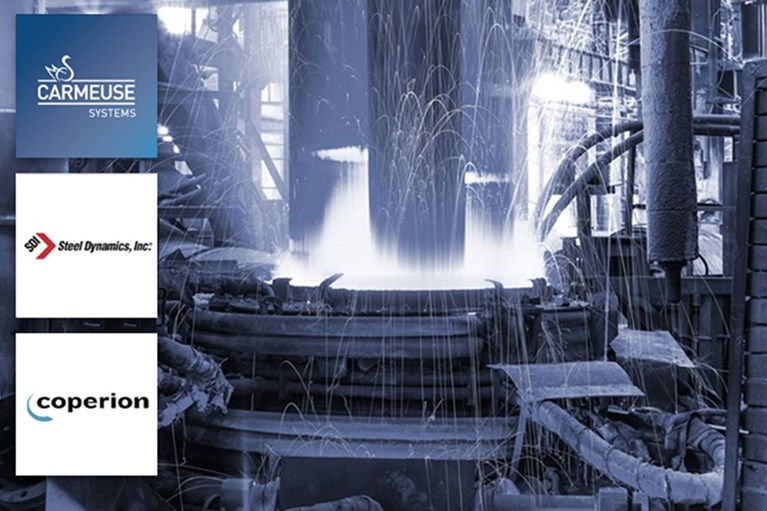
July 29, 2024
Successful Lime Injection System Installation at SDI Pittsboro
Carmeuse Systems is proud to announce the installation of state-of-the-art high calcium and dolomitic lime injection systems for Steel Dynamics, Inc. at their Pittsboro, IN location.
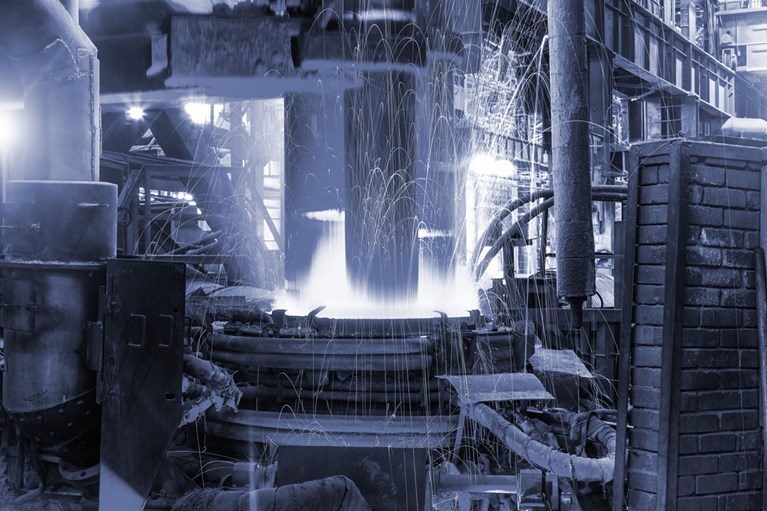
July 26, 2024
Top Considerations for Implementing & Maintaining Lime Injection Systems
Lime injection systems can play a vital role in improving operations, but proper system design and maintenance are essential.
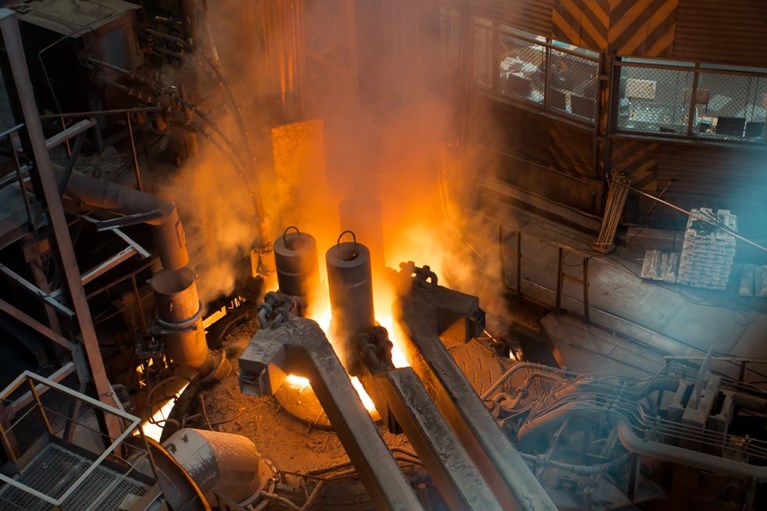
August 20, 2024
Three Ways Lime Injection Reduces Costs
Lime can have a significant impact on steel quality, metallurgical properties, productivity, and the total cost of production