PCC Production
Carmeuse Systems supports precipitated calcium carbonate (PCC) producers by providing unmatched lime handling expertise, slaking equipment, and comprehensive bulk reagent handling solutions for your operation.
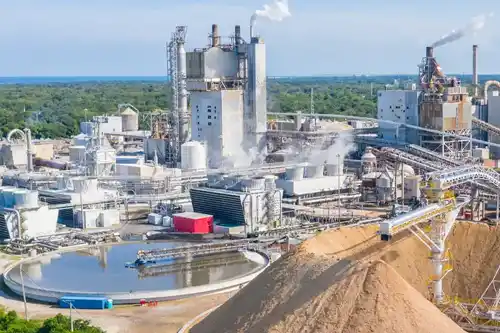
What is Precipitated Calcium Carbonate?
Precipitated calcium carbonate, or PCC, is a synthetic calcium carbonate product. It is derived from, and possesses, the same chemical formula (CaCO3) as natural calcium carbonate (limestone), but is chemically purer than natural limestone. PCC has a long commercial history. It was first produced in 1841 in England by John E. Sturge Ltd, which manufactured its ‘precipitated chalk’ by treating calcium chloride, left over from its production of potassium chlorate production, with soda ash and carbon dioxide (CO2). The milk of lime process was introduced in 1898 by same the company.
In the US, PCC production dates back to 1938 and the C.K. Williams Company of Massachusetts. Both John E. Sturge Ltd and C.K. Williams Company plants continue to make PCC today under the ownership of one of today’s largest PCC producers, Specialty Minerals Inc. (SMI).
PCCProduction
The Precipitated Calcium Carbonate Production Process
Modern PCC production utilizes the milk of lime process, which involves direct carbonation of hydrated lime slurry.
The PCC production process begins with quicklime (CaO). The quicklime is mixed with water to form a calcium hydroxide slurry (Ca(OH)2) in an exothermal chemical reaction known as slaking This slurry is then cooled and transported to a mix tank, where CO2 is added. This carbonates the calcium hydroxide slurry to produce calcium carbonate.
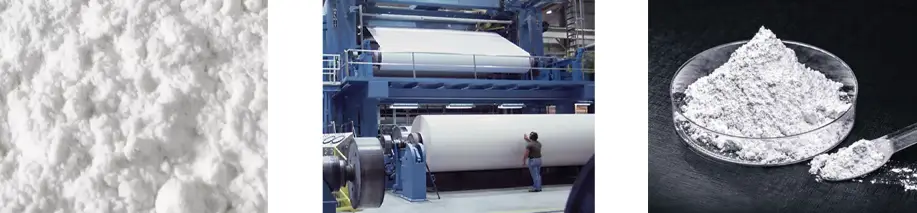
The final step in the PCC production process is to screen the calcium carbonate to remove any off-spec particle sizes. Screen sizes can be as fine as 325 mesh (44μm). The final screened product is then stored in a holding tank until needed.
The end result of this process is a calcium carbonate product that can be controlled for particle size, surface area, particle shape, and surface chemistry to meet customer specifications. PCC is also whiter and brighter than most naturally occurring calcium carbonate.
The Slaker in Precipitated Calcium Carbonate Production
The slaking reaction plays a critical role in controlling the particle size of the PCC and, alongside the subsequent carbonation reaction, is responsible for ensuring an on-spec PCC product. The hotter the slaking temperature, the finer the particle size. Combine this with cold carbonation temperatures, and very fine particle sizes are possible.
Slaking temperatures for PCC production can approach 195°F (90.6°C). This is hotter than standard slaking temperatures of 175°F to 185°F (79.4°C and 85.0°C) used in other applications. This higher temperature is necessary to achieve the required fine particle size, but runs greater risk of boiling over the slaker.
Careful management of the slaking process is needed to avoid this. A number of factors determine slaking temperature, including water-to-lime ratio, quicklime quality, consistent mixing within the slaker, and the temperature of the slaking water. All of these factors must be controlled to ensure the safe production of high-quality PCC.
In addition, the higher slaking temperature generates more steam than standard slaking reactions (where steam generation is already significant). As in standard slaking systems, this must be carefully managed by removing steam in a controlled manner to avoid any health and safety concerns, as well as the migration of steam into the dry quicklime feed systems and into the silos. This would quickly cause degradation of the quicklime and might also cause dry material handling and scaling issues.
The slaked lime slurry also needs to be de-gritted– either by vibratory screen or inclined rakes/screws – to remove any remaining impurities. This de-gritting step is a standard part of most slaking processes, but is particularly important in the PCC production process, where high-purity hydrated lime slurries are required. Screening down to 60 mesh (250μm) is possible at this stage.
Detention slakers are typically used in the PCC production process. This slaker type can produce a continuous supply of lime slurry for use downstream. Detention slakers are controlled by monitoring the temperature of the slurry and automatically adjusting quicklime and water inputs to maintain an optimum slaking temperature. As a general rule, the water-to-lime ratio will be about 4:1. Compared to other slaker types, one of the key advantages of detention slakers is their reliability and response time as it pertains to controlling slaking temperature. Detention slakers are also moderately sized, relatively inexpensive to install, and have a high ability to be optimized.
What is Precipitated Calcium Carbonate Used For?
The most prevalent use of PCC is in paper production, thus most PCC plants in the US are located next to paper manufacturing facilities. Some are even connected by pipeline to allow direct and continuous supply of PCC to the paper-making process.
We go into more detail about the use of PCC in papermaking below. However, paper is not the only use for PCC. It is also used in:
- Adhesives and sealants as a flow control additive
- Food and pharmaceuticals as dietary calcium, the base material and bulking agent in medicines and cosmetics, and as a mild abrasive and viscosity aid in toothpaste
- Paints and ink as extenders to increase hiding and reduce titanium oxide consumption
- Plastics as a filler/extender and to control flow and molding of fine components
- PVC to enhance impact strength
The Benefits of PCC in Paper Production
Precipitated calcium carbonate is primarily used as a filler to add volume, improve opacity and dimensional stability, and improve printability of the paper. The use of fillers also reduces the amount of wood fiber consumed by the paper production process.
The ideal filler material should not alter the chemical properties of the paper pulp and should have
- High whiteness
- An appropriate refractive index and particle distribution
- High retention in the paper
- Low density and abrasiveness
- Low cost
A number of mineral products can be used as fillers, including kaolin clay, ground calcium carbonate (GCC), titanium oxide, and talc. The latter two are expensive and used only in specialty applications. GCC and clay are both natural products thus do not offer the same consistency as PCC, which can be crystallized to the precise chemical and physical properties desired by the papermaker. PCC is also generally cheaper than clay fillers and delivers higher supply security, since most production is captive to the paper production process (which likewise reduces transportation costs).
PCC has a sustainability advantage too in that a proportion of the CO2 emitted during paper manufacture can be captured and used to carbonate the lime slurry (see above on the PCC production process).
OurRole
Our Role in Precipitated Calcium Carbonate Production
Carmeuse Systems is a leading expert in the design, supply, procurement, and installation of dry chemical systems. We deliver end-to-end lime handling systems: from truck unloading and material handling to the silo, and related silo safety and environmental systems. We are also a globally-recognized expert in the supply of lime slakers and auxiliary equipment, such as slurry holding tanks, de-gritting systems, and slaker control systems.
Carmeuse Systems is backed by the experience of its parent company, Carmeuse, a global leader and expert in lime products and solutions. The Carmeuse team of specialists have over a century of combined industry experience in the optimized use of lime across a range of industry applications, including the supply of quicklime for precipitated calcium carbonate production.
Our unique partnership delivers industry-leading lime products and lime handling systems, slaker selection, and system engineering and optimization. It’s a partnership that has proven itself over many years as one of the biggest producers of PCC in North America, where Carmeuse Systems and Carmeuse are the largest suppliers of slaking systems and quicklime.
Supporting Other Dry Bulk Reagents
Carmeuse Systems designs and develops chemical feed systems for a variety of dry bulk reagents. From storage and flow promotion, to conveying and dust control solutions, our engineers can work with you to develop an effective solution for your operation's application and equipment needs.
RelatedInformation