Lithium Extraction
As the demand for battery-grade lithium continues to grow, Carmeuse Systems is ready to support lithium producers by providing lime slaking equipment and dry chemical handling systems to meet your needs.
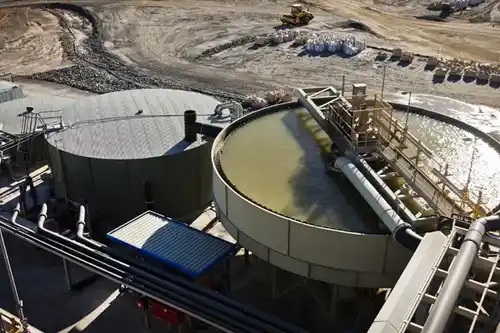
Lithium Resources
Commercial lithium extraction technology/methods currently rely on two main sources of the metal:
- Salt-flat brines
- Mineral ores, such as spodumene
As the anticipated need for domestic lithium resources rises, a number of alternative lithium extraction technologies are also creating interest. These include direct lithium solvent extraction from seawater, and geothermal and oil well brines, as well as mining of lithium-bearing clays.
LithiumExtraction
How to Extract Lithium
Conventional Lithium Brine Extraction
The majority of today’s commercial lithium production is from those that extract lithium from underground brine reservoirs (salars). Most takes place in the so-called Lithium Triangle, high-up in the Andes, where the borders of Bolivia, Argentina and Chile meet, and in China.
Lithium brine recovery is a straightforward but time consuming process. Salt-rich water is pumped to the surface and into a series of evaporation ponds. Over a period of months, the water slowly evaporates and a variety of salts precipitate out, leaving a brine with an ever-increasing concentration of lithium.
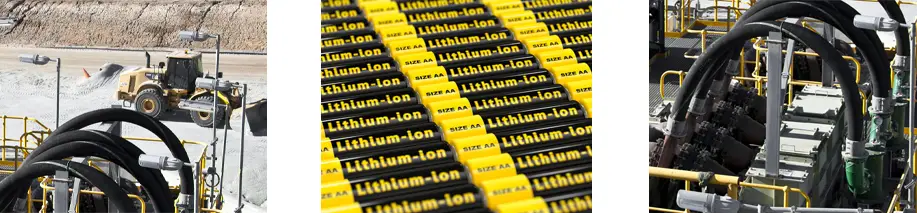
During the evaporation process, a slurry of hydrated lime (Ca(OH)2) is added to the brine to precipitate out unwanted elements, particularly magnesium and boron (as magnesium hydroxide and calcium boron salts). When lithium concentration reaches a certain point, the brine is pumped to a recovery facility to extract the metal, a process that usually includes the following steps.
- Brine purification to remove contaminants or unwanted elements.
- Chemical treatment to precipitate out desirable products and byproducts.
- Filtration to remove the precipitated solids.
- Treatment with soda ash (Na2CO3) to precipitate out lithium carbonate (Li2CO3).
- Washing and drying of the lithium carbonate into the final product.
Hard Rock Mining
Hard rock mining is a considerably more complex and energy-intensive process than conventional brine extraction. Although there are over 145 minerals that contain lithium, only five are used for commercial lithium extraction: spodumene, lepidolite, petalite, amblygonite, and eucryptite.
Of these, spodumene is the most abundant, yielding the vast majority of mineral-derived lithium. Australia accounts for much of the world’s spodumene production, with some smaller operations in Brazil, and other mineral-based lithium operations in Portugal, southern Africa and China. By 2025, additional mines are expected to be online in North America and Finland.
After the ore is mined, it is crushed and roasted at 2012°F (1100°C). It is then cooled to 140°F (65°C), milled and roasted again, this time with sulfuric acid, at 482°F (250°C), a process known as acid leaching. During this last step, the hydrogen in the sulfuric acid is replaced with lithium ions, to produce lithium sulfate and an insoluble residue.
As in brine-based lithium extraction, lime is added for the removal of magnesium (a constituent element in spodumene), and soda ash is used to precipitate lithium carbonate from the final purified, filtered solution. Lime slurry may also be used as a pH adjuster to neutralize excess acid from the acid leaching process.
New Lithium Production Methods
According to the USGS, the only commercial-scale lithium production in the US comes from a brine operation in Nevada (there is also a lithium battery recycling facility in Lancaster, OH, as well as lithium processing plants). However, there is growing pressure to increase domestic lithium production to help secure supplies of this critical metal.
Opportunities exist for direct lithium extraction, notably from geothermal brines from the Salton Sea, CA, and so-called 'produced water' from shale gas fracking in Texas. A number of companies are also actively looking into extracting lithium from lithium-bearing clays, notably in Nevada. Several different production methods are being tested, including acid leaching in both sulfuric acid and hydrochloric acid.
Any use of acid leaching is likely to need a base material, such as hydrated lime, for removing impurities and neutralizing waste before its return to the natural environment.
Lithium Carbonate vs Lithium Hydroxide
The end product of both brine and mineral-based lithium extraction technology is most often lithium carbonate. Other common commercial lithium products include:
- Lithium Hydroxide (LiOH) - Lithium Hyrdoxide is used most often for making lithium salts
- Lithium Chloride (LiCl) - Lithium chloride is mainly used for the production of lithium metal
- Lithium Bromide (LiBr) - Lithium Bromide is most often used in air-conditioning systems as desiccant
- Butyllithium (C4H9Li) - Butylithium is mainly used as a strong based in organic chemistry
- Pure Lithium Metal - Pure Lithium Metal is often used for rechargeable batteries in things like phones or laptops
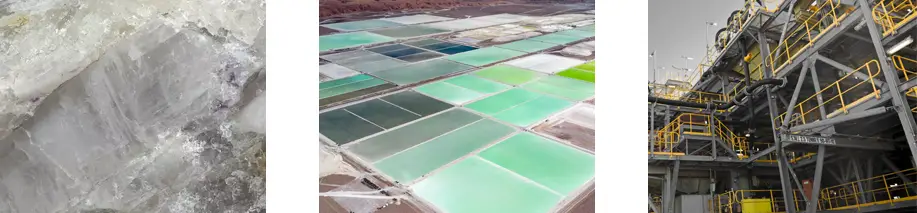
Lithium carbonate has a range of industrial uses: from battery manufacturing to the production of flooring treatments, cement densifiers, adhesives and glazes. It is widely used as a grease and lubricant, and is an essential medication (as listed by the World Health Organization). It can also be easily converted to lithium hydroxide, which is fast becoming the preferred
lithium compound for electric vehicle manufacturers, since it allows the manufacture of higher-performing, longer-lasting batteries.
The conversion process involves adding hydrated lime to lithium carbonate. Lithium ions then effectively ‘swap places’ with the calcium in the lime to produce lithium hydroxide and a solid calcium carbonate (CaCO3) residue, which is straightforward to remove by filtration or settling.
OurRole
Our Role
As a specialist in the design, procurement and installation of dry bulk chemical systems, we are well-placed to support lithium producers with their dry chemical handling needs. We have particular expertise when it comes to storing and handling dry chemical products, such as quicklime (CaO) and soda ash.
We are also a leading expert in the supply of lime slakers, which take quicklime and turn it into hydrated lime slurry so it can be added to the lithium extraction process.
Optimizing the quality of the hydrated lime slurry – its purity and reactivity – offers lithium producers the opportunity to improve the overall effectiveness and efficiency of their lithium production process. A lot can be done in this regard simply by selecting the right lime slaker. With our experience in this area, we are able to support lithium producers when it comes to making the best lime slaker choice for their operational needs.
The quality of the lime slurry is also in the spotlight, as automakers look for higher-purity lithium resources in their quest for batteries that drive further. Lime is one route in which impurities can find their way into lithium products, notably aluminum, which commonly occurs in limestone, but is one element that lithium producers work hard to remove. A modern lime slaking system will help to remove such impurities, providing a high-purity hydrated lime slurry. At Carmeuse, research and development is also currently ongoing to further improve the rejection of non-process elements in the slaker for the production of even higher purity hydrated lime slurries.
Supporting Other Dry Bulk Reagents
Carmeuse Systems designs and develops chemical feed systems for a variety of dry bulk reagents. From storage and flow promotion, to conveying and dust control solutions, our engineers can work with you to develop an effective solution for your operation's application and equipment needs.
RelatedInformation
Related Information
Frequent Question About Lithium
Lithium brine extraction is a straightforward but lengthy process. It involves drilling wells to access underground brine deposits, which are then pumped to the surface and distributed to evaporation ponds. The brine is left to evaporate, concentrating the lithium. Once the desired concentration is achieved, the brine is processed to extract lithium carbonate or hydroxide [1].
Lithium is harvested from both brine and hard rock sources. In brine extraction, the lithium-rich brine is pumped to the surface and allowed to evaporate in ponds. In hard rock mining, spodumene ore is mined, crushed, and processed to extract lithium [1].
Lithium is separated from other materials through chemical treatments that remove impurities and concentrate the lithium solution [1].
Lithium mining involves extracting lithium from brine or hard rock sources. The extracted lithium is then processed to produce battery-grade lithium products [1].
Lithium is extracted from brine by pumping the brine to the surface, evaporating it in ponds, and processing the concentrated solution to extract lithium carbonate or hydroxide [1].
Lithium is collected from brine or ore through extraction and processing methods [1].
Lithium is extracted from the earth through brine extraction or hard rock mining [1].
A lithium leach field works by using chemicals to dissolve lithium from its ore, which is then processed to extract lithium.
Lithium mines work by extracting lithium from brine or ore and processing it to produce high-purity lithium products [1].
We get lithium from the earth by extracting it from brine or ore and processing it to produce lithium carbonate or hydroxide [1].
We get lithium by extracting it from brine or ore and processing it to produce high-purity lithium products [1].
Lithium is produced by extracting it from brine or ore and processing it to produce lithium carbonate or hydroxide [1].