Iron & Steel
Carmeuse Systems is able to provide advanced lime injection systems and lime handling equipment to meet the needs of Electric Arc Furnace (EAF) steelmakers.
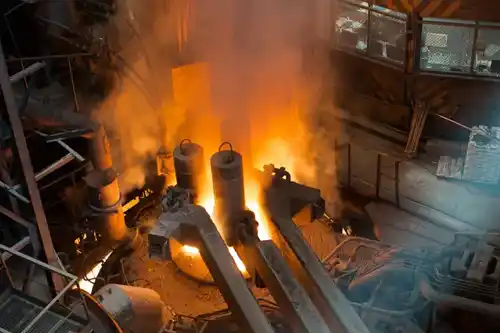
How is Steel Made?
Modern steelmaking comprises of two main technologies: basic oxygen furnaces (BOF) and electric arc furnaces (EAF).
BOF steelmaking uses primary raw materials – iron ore and coal – to produce new steel. Iron ore is initially reduced to liquid iron (hot metal) in the blast furnace. The hot metal is then converted to steel in the BOF. About 70% of global steel production is attributed to this method of steelmaking.
In contrast, the primary feedstock for the EAF steelmaking process is recycled scrap steel, although direct reduced iron (DRI) and hot metal (pig iron) can also be used as secondary charge materials when scrap availability is limited or when the scrap contains a high amount of impurities. The charge is melted in the EAF using high-current electric arcs, which is then processed into new steel products. EAF steel production accounts for about 30% of global steel production.
EAF steelmaking plants tend to be smaller and less expensive than integrated BOF steelmaking plants, which are generally only cost-effective at large scales (millions of tons per year). EAF steelmaking is also a more flexible process, able to scale up and down as the market requires. And despite consuming significant amounts of electrical energy during the melt phase, EAF steelmaking is more energy efficiency than primary BOF steelmaking. It is thus often touted as a critical technological pathway for decarbonizing steel.
HowisLimeUsed
The Uses of Lime in EAF Steelmaking
Lime is used in both EAF and BOF processes as a fluxing agent. It also has a role in protecting the refractory lining from chemical corrosion.
Lime as a Fluxing Agent
Fluxing agents are chemicals added to the steelmaking process to aid in slag formation. Steelmaking slag has a couple of important roles. Firstly, it protects the surface of the melt and helps reduce oxidation, and it also facilitates the removal of impurities. Both roles help improve the quality of steel produced.
Lime is widely used as a flux due to its ability to bond with common impurities in the steel (e.g., silica, phosphorus, sulfur) and aid in efficient and effective slag formation. The slag has a lower density than steel and therefore floats on top of the molten steel, where it prevents direct contact between the molten steel and ambient air. This reduces undesirable oxidation of the melt. The slag – and the impurities it contains – are then skimmed off to leave a purer melt.
How Does Dolomitic Lime Extend Refractory Life?
Any equipment involved in high-temperature industrial processes will be protected by a refractory lining. This protects the equipment from exposure to extremely high temperatures. With steel melting at about 2,732°F (1,500°C), the temperatures required inside an EAF are among the highest of all industrial processes.
This requires a robust refractory, but it is not just the temperature that poses a challenge to EAF linings. The refractory must also be resistant to any mechanical impact occurring when the furnace is charged, as well as to the corrosive chemistry of the slag, which tends to dissolve the magnesium oxide (MgO) in furnace refractories.
On this latter point, lime has an important role to play via the emergence of foamy slag practices. Foamy slags are produced via the addition of dolomitic lime during the melt process. Because dolomitic limes offer an alternative source of MgO, the slag dissolves less of the magnesium oxide in the refractory. This extends the operating life of the lining and protects against the risk of refractory failure and consequent damage to the EAF.
DirectLimeInjection
Direct Lime Injection
What is Direct Lime Injection?
There are a number of ways that lime can be added to the EAF. Traditional methods include charging it with the scrap, or discharging it directly into the furnace through a hole in the furnace roof (fifth-hole addition), or via super-sack drops. However, there are drawbacks to these techniques, most notably when it comes to the release of lime dust into the melt shop and the inability to precisely control lime addition.
Direct lime injection was developed to overcome these issues. It provides a clean, efficient and controllable method of adding lime into the EAF. The advantages of direct lime injection into the EAF include the following:
Lime Injection Eliminates Dust Emissions
From truck unloading to the point of feeding into the EAF, direct lime injection is a closed system. This eliminates the potential for lime dust emissions into the melt shop: a particular issue with super sack drops. Fifth-hole addition reduces, but does not completely prevent, dusting.
Eliminating lime dust emissions not only improves health and safety in the melt shop. It also reduces the load placed on the baghouses that provide environmental control – with benefits for both baghouse cleaning/maintenance and waste disposal costs.
Lime Injection Reduces Lime Consumption
Eliminating dusting also reduces overall lime consumption. This is because no lime is lost during handling and feeding operations; it all ends up where it is supposed to go – in the EAF.
Lime Injection Improves Slag Formation
With lime injection being a closed system and all of the product going into the furnace, direct lime injection utilizes finer lime particles than other techniques. These finer particle sizes dissolve faster into the melt thus building slag more quickly.
In addition, direct lime injection is a much more accurate and controllable process, resulting in an improved slag chemistry and helping to achieve an effective foamy slag. The efficient use of lime and better control of slag chemistry have led to significant energy savings for steelmakers.
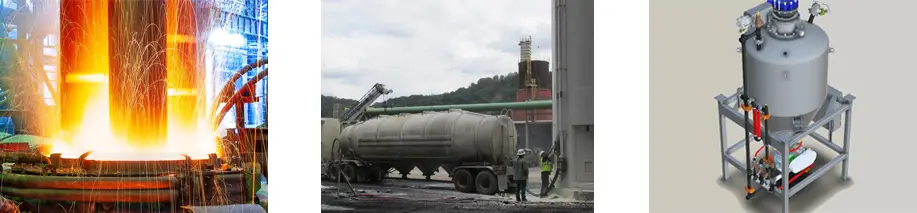
OurRole
Our Role in EAF Steelmaking
Carmeuse offers an end-to-end solution for both greenfield and retrofit direct lime injection systems: from lime products through our parent company, to truck unloading to silo storage, flow promotion and feeding into the EAF. This includes pneumatic dense-phase conveying via our strategic partnership with Coperion.
Carmeuse Systems has 50+ years of experience in pneumatic conveying systems. Whether you are building a new plant, adding lime injection to a current EAF furnace, or upgrading an existing lime injection system, we can accommodate your needs. Our technical experts will visit your site, perform an evaluation, inspect existing equipment, understand your needs, and then provide you with a custom system designed to achieve your goals. Whether the pressure vessel will sit below the silo, adjacent to the silo, or a long distance away, our engineers can design a layout that fits your site requirements.
To get lime efficiently to the furnace, it starts with an understanding of the source. Carmeuse Systems draws on the raw material expertise from its parent company Carmeuse, a global leader in lime products, to ensure that your system is designed to accommodate the high calcium or dolomitic lime available to your plant. The Carmeuse team of specialists have over a century of combined industry experience in the optimized use of lime products.
Supporting Other Dry Bulk Reagents
Carmeuse Systems designs and develops chemical feed systems for a variety of dry bulk reagents. From storage and flow promotion, to conveying and dust control solutions, our engineers can work with you to develop an effective solution for your operation's application and equipment needs.
RelatedInformation