Flow Aids & Feeders
Rotary Airlock Valve Feeders
Rotary airlock valves, also known as rotary airlocks or rotary valves, are key components in handling dry bulk materials. These valves control the flow of materials between chambers. They also stop air from leaking, which helps ensure safe and efficient operation. Choosing the appropriate rotary airlock valve is vital for ensuring a smooth and dependable operation within your facility. We take pride in the meticulous care we provide to each valve that we sell either individually or as a part of our systems.
We have over fifty years of experience in designing dust collection and pneumatic conveying systems. Our engineering skills allow us to find the best rotary valves for your airlock and feeding needs. We prioritize understanding your specific processes and applications, enabling us to confidently suggest the optimal solution tailored to your material processing challenges.
Our rotary airlock valves can handle many types of materials. They work well with fine powders and large granules. This makes them versatile and reliable for different industrial uses.
Manufacturers make each rotary airlock valve with care to maintain tight clearances between the rotor and barrel. This helps reduce air leakage and improve the system's efficiency. The robust construction of our rotary airlock valves ensures durability and longevity, even in the most demanding environments. Additionally, we equip our valves with outboard bearings to protect against contaminants, which further extends their service life.
We understand that every operation is unique, which is why we offer customizable options to meet your specific needs. Whether you need a standard rotary airlock valve or a special solution, our team is here to help. We focus on providing high-quality products and great customer service. Count on us to provide rotary airlock valves. They will improve your material handling processes and help your operations succeed.
Documentation
Documentation
Data Sheets
For additional information or to discuss your requirements with our sales group, please contact us.
Why Choose an Industrial Rotary Airlock Valve From Carmeuse Systems?
Carmeuse Systems understands rotary airlock valves play a crucial role in the performance of your bulk material handling and pneumatic conveying systems. Selecting the correct rotary airlock valve is key to maintaining a productive and reliable plant operation. We pride ourselves on the attention we give every valve that leaves our shop.
Our 50 plus years of experience in the design of both dust collection and pneumatic conveying systems, as well as, the design and manufacture of rotary airlock valves, provides us with the engineering expertise to understand which type of rotary valves will best meet your airlock and feeder needs. We make it our priority to understand your processes and your applications so we can confidently recommend the right solution that best addresses your material processing needs whether it be a new valve or the need to refurbish and repair an existing valve.
AvailableValves
Available Rotary Airlock Valves
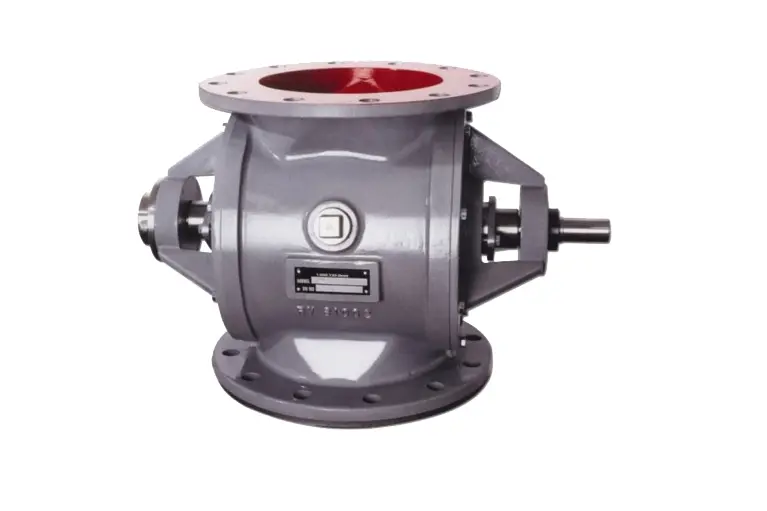
RV Series - Rotary Airlock Valve
This valve is ideal for the pneumatic conveying of dry, free flowing, noncohesive bulk density products or powders. This round flange, drop-thru valve feeds material through the ten rotating vanes where it drops out the bottom outlet flange via gravity. This outboard bearing rotary airlock valve achieves high fill efficiencies with minimum air leakage, due to precise machining and tight rotor clearances. The RV Series Rotary Airlock Valve is available in sizes from 6” up to 14”.
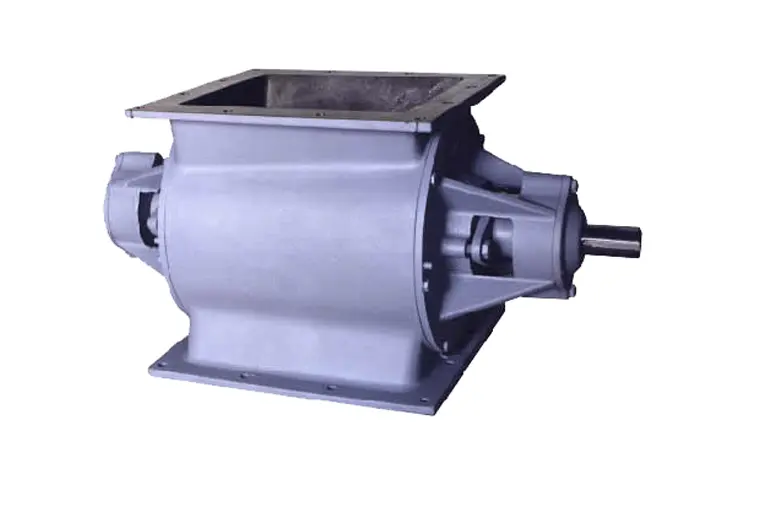
RVS Series - Rotary Airlock Valve
This valve is ideal for the pneumatic conveying of dry, free flowing, noncohesive bulk density products or powders. This square flange, drop-thru valve feeds material through the six rotating vanes where it drops out the bottom outlet flange via gravity. This outboard bearing airlock (valve) achieves high fill efficiencies with minimum air leakage, due to precise machining and tight rotor clearances. The RVS Series Rotary Airlock Valve is available in a 12” size.
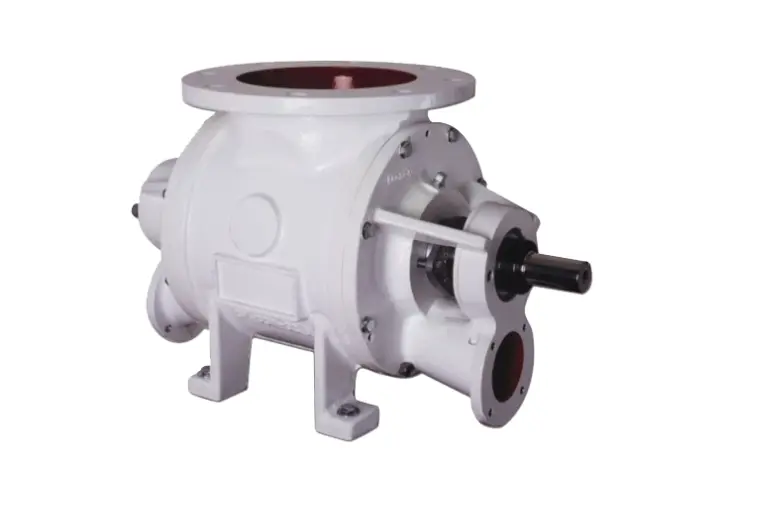
CV Series Conveying Rotary Airlock Valve
The CV Series Conveying Rotary Airlock Valve is designed to handle most types of dry granulated materials including difficult, sticky products in pneumatic conveying systems with conveying pressure up to 15 psi. This outboard bearing airlock has ports on the sides of the end covers that connect directly to the convey line pipe. The conveying air blows through the rotor pockets to assist the material to discharge directly into the conveying line. The CV Series Conveying Rotary Airlock Valve is available in two sizes, 8” and 12”.
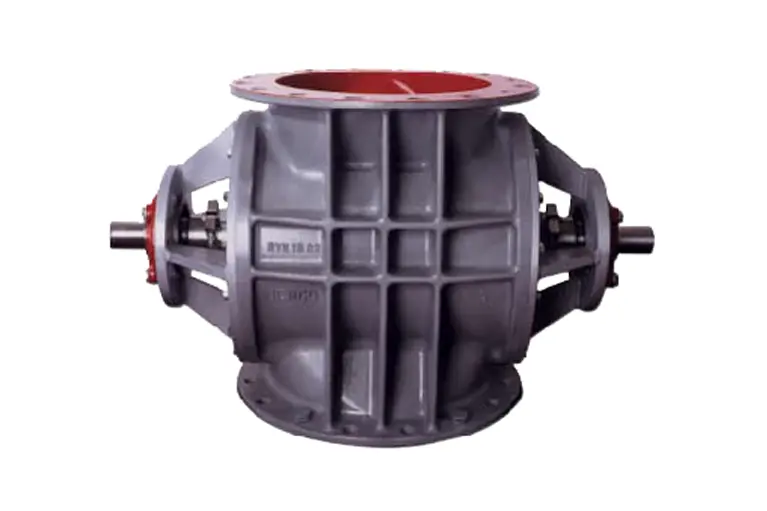
RVH Series - Heavy Duty Rotary Airlock Valve
The RVH Series Heavy Duty Rotary Airlock Valve is designed and constructed for high volume service such as in petrochemical and mineral processing plants.
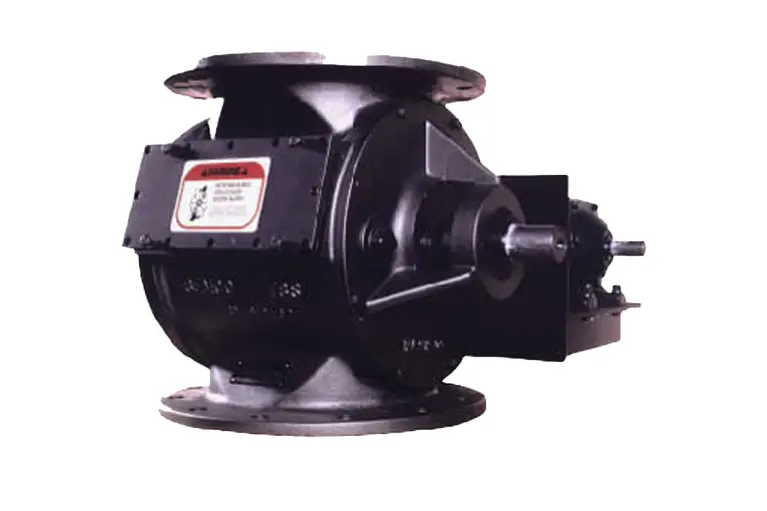
RVI Series - Abrasive Service Rotary Airlock Valve
The RVI Series Abrasive Service Rotary Airlock Valve is precision made with a heavy duty cast body and rugged fabricated design. It is designed as a feeder valve for dry, bulk material in applications where close tolerances are necessary in demanding high pressure - high vacuum services. A bolted removable inspection panel and threaded plugs in both end plates allows for in-place serviceability of replacement blades.
Features&Benefits
Rotary Airlock Valve Features & Benefits
The features and benefits of our rotary airlock valves and feeders include:
- A variety of designs provides options addressing your specific needs.
- Cast iron construction offers rugged design providing maximum structural stability.
- Precision-machined housing minimizes rotor-to-barrel clearances, limiting leakage.
- Outboard bearing design protects bearings from contaminants extending maintenance cycles.
- Packing gland type seals makes for easy maintenance saving on costs.
- Open throat valve inlet design ensures material flows to rotor pockets maximizing performance.
- Handles pressure differentials up to 15 psi making it well suited for pneumatic conveying operations.
- Chain and sprocket drive offers a smaller footprint and greater speed selection providing flexibility to the applications being used in your process.
To discuss the features and benefits of specific rotary airlock valves we provide and the typical bulk materials processed, please see our documents section for individual data sheets which include drawings, specifications, and more.
Key Considerations for Rotary Airlock Valve Selection
Selecting the right rotary airlock valve for your dry bulk material handling and pneumatic conveying systems is essential. Several key considerations need to be taken into account when selecting rotary airlock valves:
- Type of bulk material being processed
- Type of application
- Operating temperature
- Level of abrasion resistance required
- Material density and moisture levels
Sizing and Valve Design Considerations
Selecting the right valve size and design is critical to running your feeding and metering systems safely and efficiently while minimizing pressure loss. When selecting your valve, consider the following:
- If clearances are not set correctly, air can leak through the valves. Air loss through the valve can contribute to inadequacies in feed rate capacity, create unstable flow conditions, create blockages in conveying line and cause excessive wear on the interior surfaces. Pressure, rotor clearances and material properties are all contributing factors to the amount of rotary valve leakage.
- Maintaining a constant vacuum or air pressure differential between the inlet and outlet ports while continuously moving material is critical to proper functioning of a rotary valve.
- For abrasive applications, hard chrome interior surfaces are necessary.
- Open end rotors are typically used for abrasive materials. With open end rotor design, the material encounters the housing bore and the inside surfaces of both end plates.
- Closed end rotors are used for handling pellets. In a closed end rotor design, the only blade area that is affected is the blade tip adjacent to the housing bore. The housing end plates are not affected.
Capabilities
Capabilities for Rotary Airlock Valves
Carmeuse Systems has experts that are able to assist you with any issue in your lime or dry bulk reagent handling system. If you are experiencing flow promotion issues, our team of experts can assess the issues at hand and provide solutions to ensure that your system continues to run smoothly. Carmeuse Systems can provide a flow promotion solution that suits your needs and the needs of your system.
Related Parts & Services
Related Content
FAQS
Material is fed from a silo hopper through the valve’s inlet and dropped into a rotor pocket. As the blades rotate, material is carried in the rotor pockets toward the outlet of the valve. Shaft seals prevent material and air leakage into or out of the valve ensuring a proper airlock and uniform feed.
An incorrectly sized rotary valve can result in poor efficiency, extra maintenance and operator hours, product degradation, frequent wear and tear and equipment replacement and decreased production due to frequent shutdowns.
A rotary airlock capacity is calculated using the fixed volume of the rotary valve cavity (at 100% fill efficiency) and that volume when one full revolution of the blade is made. You then obtain a “volume per revolution” in either ft3/rev or m3/rev to help calculate the capacity in lbs./hr. or kg/hr.
Now consider the following calculation:
CAP = Rotary airlock valve capacity in lbs./hr. [kg/hr.]
BD = Bulk density of the product going through the rotary valve in lbs./ft3 [kg/m3]
V = Volume of rotary airlock valve based on one complete cycle of the rotor ft3/rev [m3/rev]
EF = Fill efficiency of the rotary airlock valve, in percent
SP = Rotational speed of the rotary airlock valve, in RPM
CAP = BD x V x EF x SP x 60 (min/hr.)
Example: Require a capacity output of 19,000 lbs./hr. [8,618 kg/hr.] for quicklime at 55 lbs./ft3 [881 kg/m3] with a fill efficiency or 85%. Now, it should be considered that a rotary airlock valve should be operating at a max speed approximately 20 RPM to maximize its fill efficiency. Also, we need to consider the upstream and downstream equipment connections for the rotary valve. Assuming an 8” connection size is best; we can evaluate the size of an RV-308:
BD = 55 lbs./ft3
V = 0.3 ft3/rev
EF = 0.85
SP = 20 RPM
CAP = 55 x 0.3 x 0.85 x 20 x 60 min/hr. = 19,800 lbs./hr. [8,981 kg/hr.]
Therefore an 8” rotary valve would be well suited for the application.