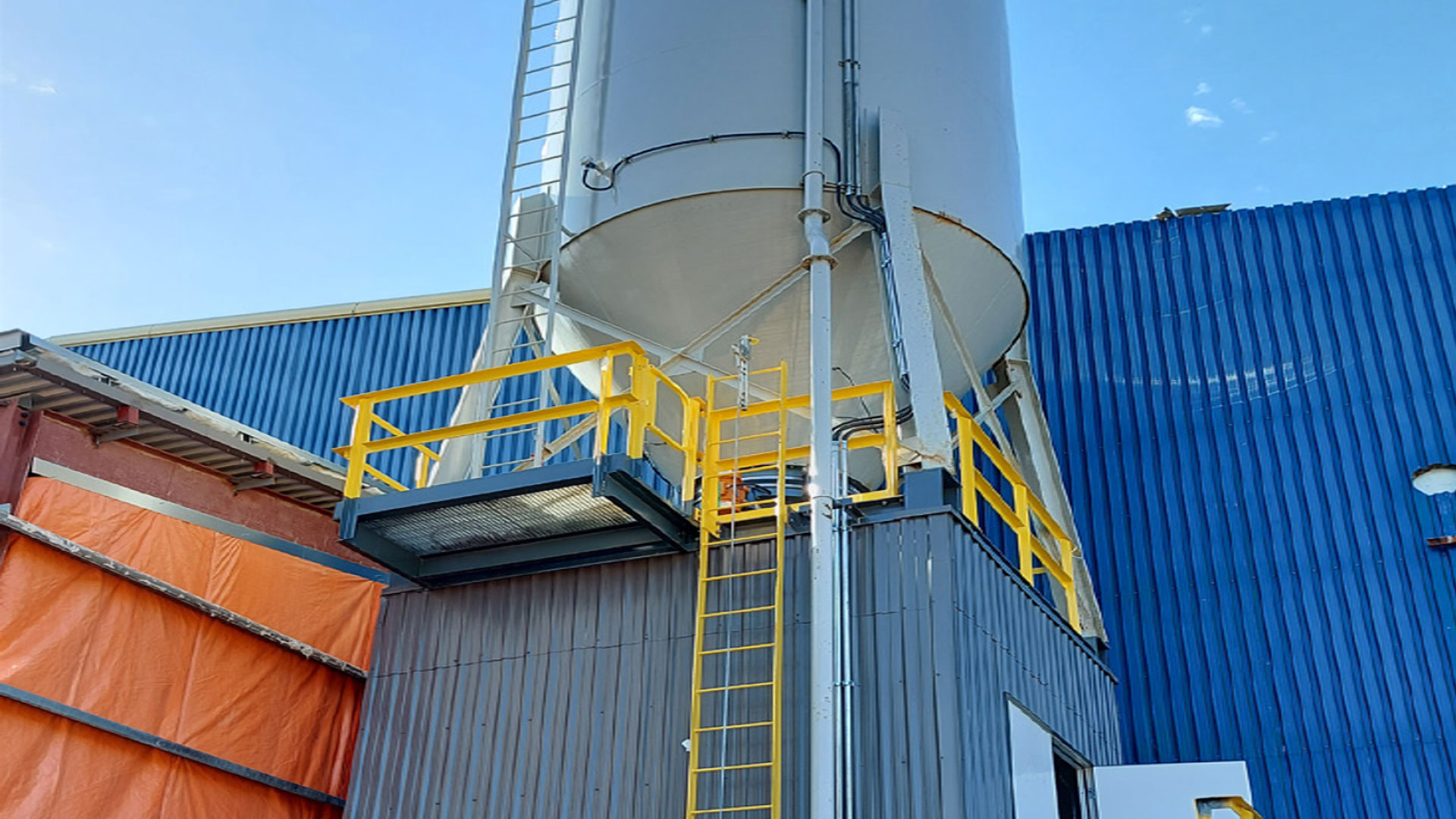
Standard Quicklime Feed System
Standard Quicklime Feed System in a Box
Integrated Silo, Feed, & Dust Collection System in a Box
The standard quicklime feed system from Carmeuse Systems is designed as a compact ”slaker-in-a box” system. This modular chemical feed system provides an integrated solution for receiving, storing, feeding, slaking and delivering up to 2,500 lb/h of quicklime from truck to the point of application. The three-piece modular design includes a 12 ft. storage silo with a bin vent filter, a ZMI Portec detention slaker module on the upper level, and a slurry storage tank module on the lower level under the lime silo.
This “plug-and-play” type system limits the amount of onsite work required reducing the construction time needed once the system arrives to your site. Carmeuse Systems assembles, installs, pipes, wires, and integrates all components/equipment through an automated control panel at our facility prior to shipment. The two modular boxes are shipped pre-insulated and upright. The upper storage silo module is shipped separately for simple connection at site.
Watch How a Chemical Feed System Functions
This video depicts the Standard Quicklime System
TYPICAL BULK MATERIALS PROCESSED
- Quicklime
TYPICAL APPLICATIONS
- Water Treatment
- Chemical Processing
- Mining
- Oil and Gas
- Pulp and Paper/Precipitated Calcium Carbonate (PCC)
Features And Benefits
Features | Benefits |
---|---|
Compact, “slaker-in-a box” system | Saves money and decreases equipment footprint enhancing plant utilization |
Fully engineered and integrated silo, feed, and dust collection system | Receives, stores, feeds, slakes and delivers quicklime to application point optimizing material handling efficiency |
Pre-assembled, piped, wired and factory tested | Reduces field installation costs and commissioning time ensuring a seamless start-up |
Three-piece ‘plug-and-play’ design | Minimizes the amount of onsite assembly required saving on labor costs |
12’ square (box) footprint | Requires no escort or pilot car to transport and has 25% more space than a conventional 12’ silo design optimizing equipment footprint |
Single-piece welded silo construction (12’-0” in diameter) | Ships preassembled limiting the amount of onsite construction needed |
Low-profile, top access, bin vent filter dust collector mounted on roof | Removes particles from the air minimizing dust emissions improving air quality and employee safety |
Skirted interior lighting, ventilation, heating and insulation | Use in cold temperature regions provides flexibility in using similar systems across multiple locations |
Complete automatic control system with PLC | Improves productivity limiting downtime adding value to the bottom line |
ZMI Portec Detention Slaker | Produces a highly reactive lime slurry maximizing lime usage. |
Lower equipment modules shipped up-right | Reduces the chance for damage during shipment allowing for faster installation and start-up |