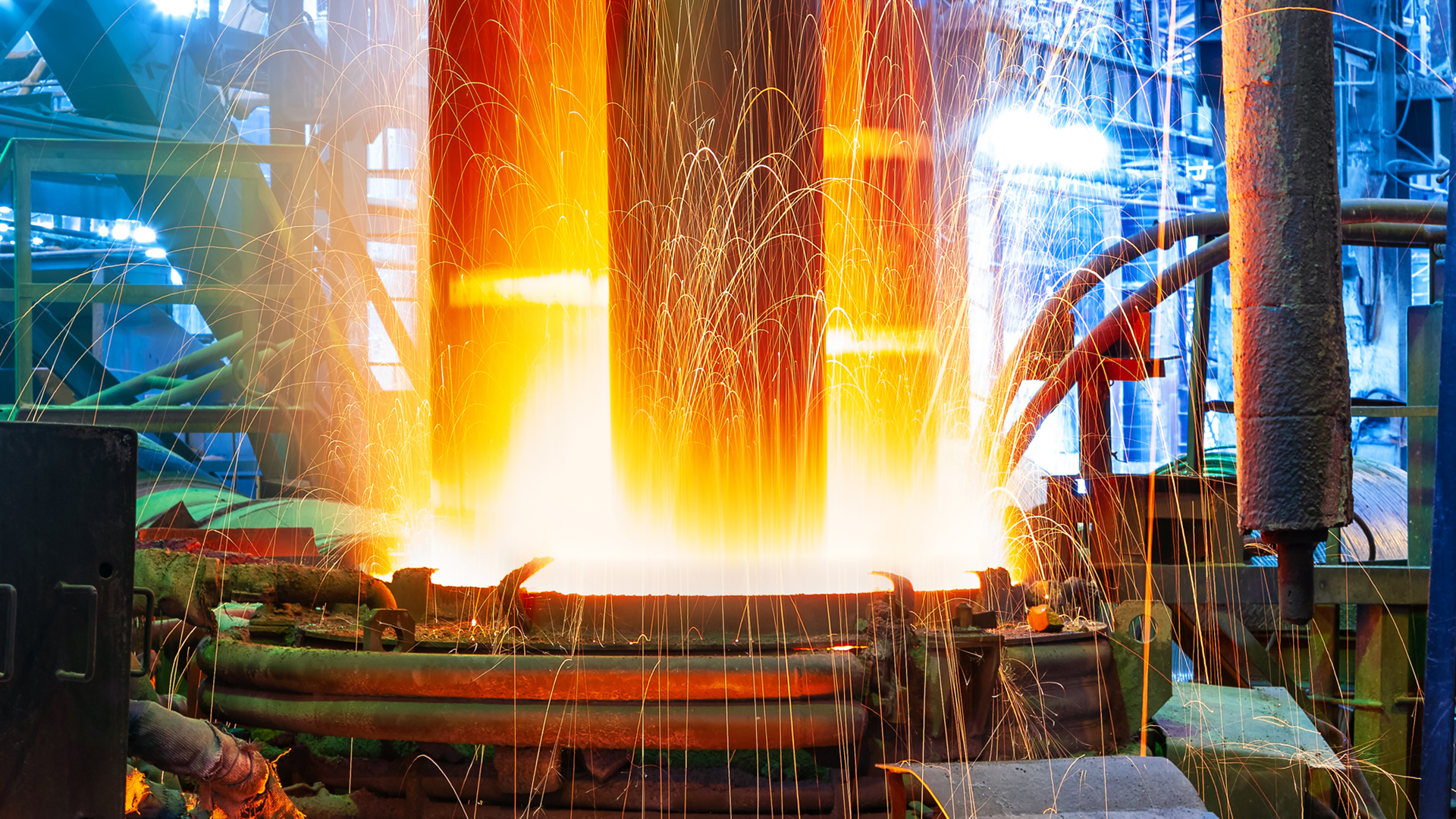
Systems
Lime Injection Systems
Lime injection systems continue to increase in popularity as any new furnace is designed with one, existing furnaces continue to be retrofitted and older systems are upgraded. The benefits can be quickly realized.
About Lime Injection
Historically, steelmakers have experimented with various methods for adding lime to the EAF including scrap bucket discharge, fifth-hole addition through the roof, super sack drops and lime screening, and briquetting. However, many of these techniques create significant environmental issues with the lime dust along with waste through the baghouse.
The emergence of the foamy slag practice to protect the furnace sidewall and refractory created a need to efficiently introduce lime during the melting process. It is highly desirable that lime is added to the process at the right time and in the right position within the furnace. Lime injection can be implemented for both high-calcium and dolomitic lime applications.
A lime injection system now provides reliable technology for steelmakers.
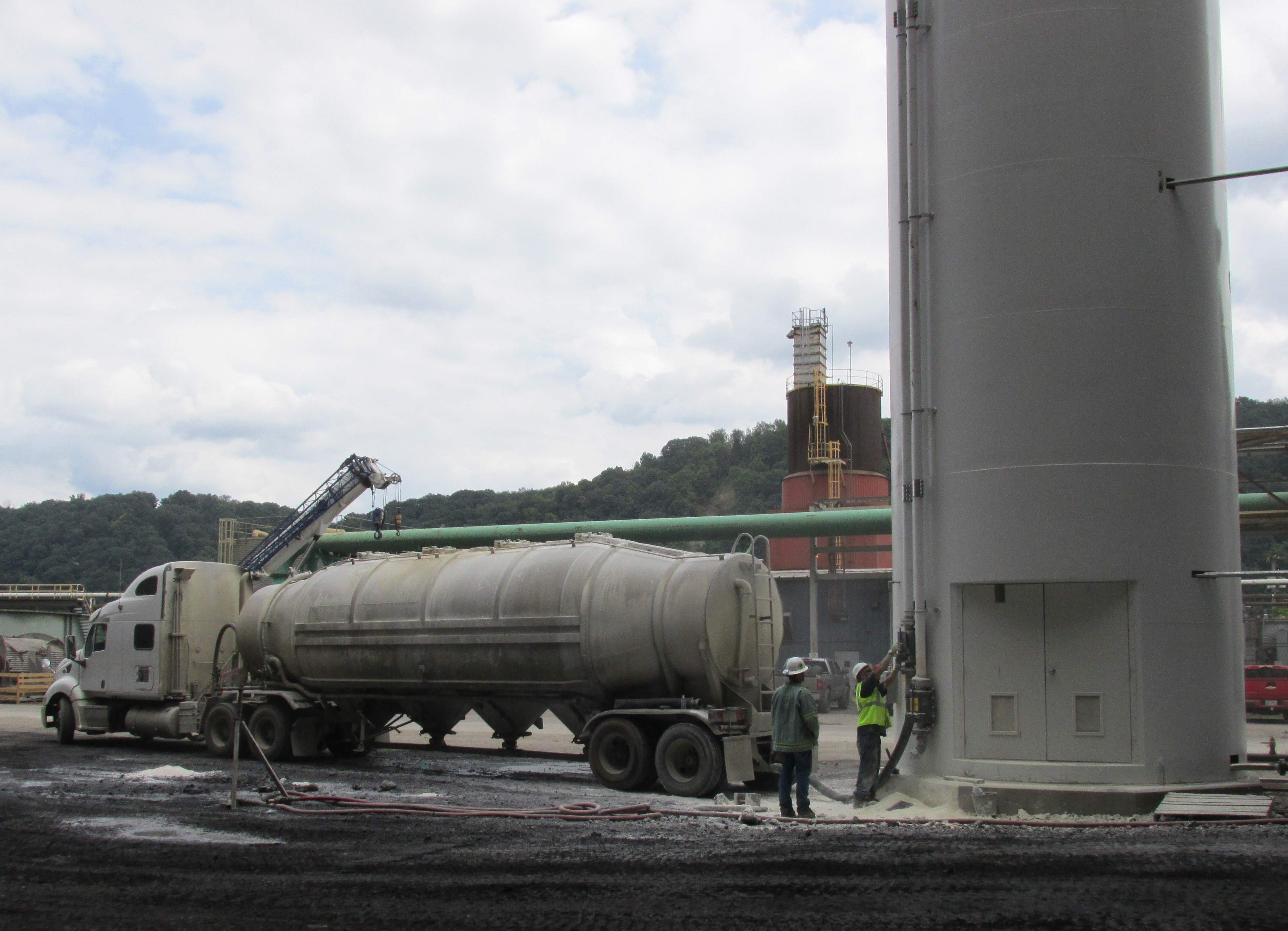
Benefits of Lime Injection
Utilization of a lime injection system results in many benefits and is now a well-established practice in the EAF steelmaking process. Lime injection provides more efficient use of lime with many steel plants seeing a 7-15% reduction in lime use due to 100% of lime being used in the process and not lost. Steelmakers also have better control of slag chemistry which leads to energy savings, flexibility in controlling slag characteristics throughout the heat, and improved steel process performance.
Additional benefits include cleaner environments for shops, reduced volumes in lime-to-furnace evacuation systems, better lime yield resulting in less quicklime used during the melting process, and reduced maintenance cost compared to mechanical systems. An added benefit includes a safer working environment due to less lime dust in the air or around the shop floor.
How Can Carmeuse Systems Help?
A lime injection system consists of many different components that must work together for reliable and efficient performance. Depending on your specific needs, a system from Carmeuse Systems can consist of everything from the point of truck offloading up to the injection block/nozzle. This includes:
- Storage Silo complete with Truck Fill Line, Pressure/Vacuum Relief Manway and Flow Promotion Components
- Mechanical or Pneumatic Conveyance System – depending on site needs
- Pressure Vessel/Bottle – for proper lime injection flow rates
- All necessary Piping and Valves
- Automation and Controls
- Replacement Parts
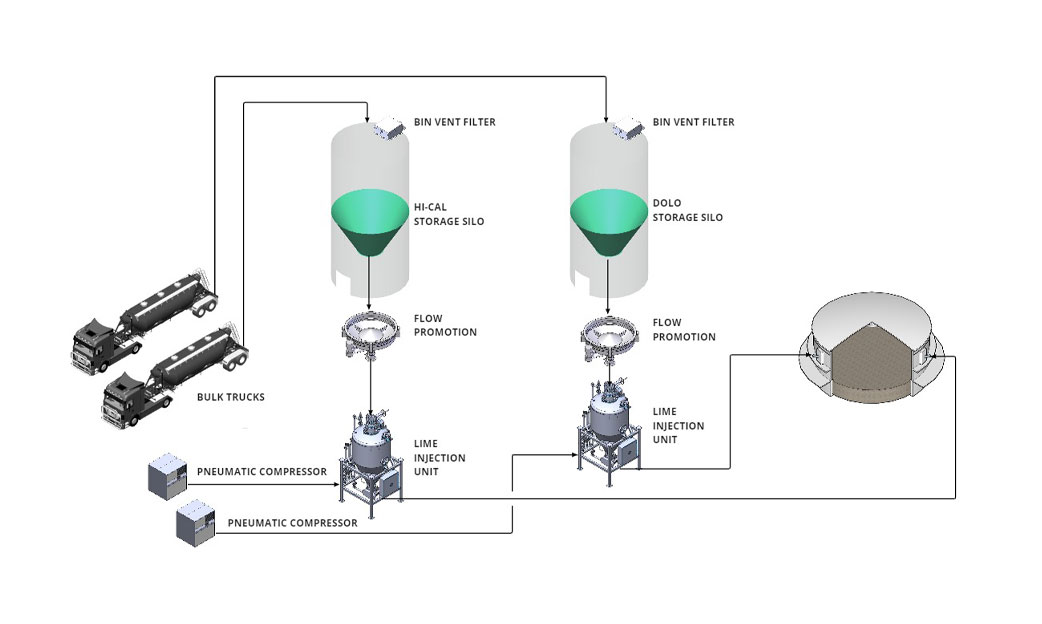
Our Capabilities
Carmeuse Systems has 50+ years of experience in pneumatic conveying systems. Whether you are building a new plant, adding lime injection to a current EAF furnace, or upgrading an existing lime injection system, Carmeuse Systems can accommodate your needs. Our technical experts will visit your site, perform an evaluation, inspect existing equipment, understand your needs, and then provide you with a custom system designed to achieve your goals. Whether the pressure vessel will sit below the silo, adjacent to the silo, or a long distance away, our engineers can design a layout that fits your site requirements.
Throughout the process, we will work with your preferred onsite installation contractor(s) to ensure the lime injection system is properly installed. Scope and drawings will be provided for sign-off so that all expectations are met.
During startup, we will be onsite to ensure everything goes as planned, answer any questions, and make necessary adjustments. After startup, Carmeuse Systems will continue to be there offering maintenance support, systems reviews, system optimization studies, operator training, troubleshooting and spare parts.
Benefits of a Lime Injection System
What makes the Carmeuse Systems lime injection system unique is the partnership that exists between Carmeuse Systems, Carmeuse, Coperion, and Tallman Technologies to provide a complete world class lime injection solution. Our experience starts with the raw material, through logistics, to the point of application, and beyond. This combination of market knowledge has evolved us to be your end-to-end solutions provider.
Carmeuse, our parent company, is one of the global leaders in lime manufacturing. Thus, our lime expertise expands across chemical and physical properties, production, sizing, testing, and application, which ensures that your lime will be used in the most efficient ways. Carmeuse works closely with EAF steelmakers to achieve optimal slag chemistries supported by the addition of lime. And this knowledge-carry-over to lime sizing is specifically matched to the injection system for optimal performance.
Carmeuse Systems provides the components of lime handling systems that include truck offloading, silo storage, pneumatic conveying, controls, and piping up to the injection nozzle. Our lime injection systems are designed to minimize lime loss during delivery to the furnace, offer better control of slag, eliminate dusting, and reduce maintenance needs. Design and installation can be in new sites or integrated into existing sites.
Coperion, formerly known as Schenck Process, is a global leader in conveying processes. Coperion is our partner for the dense phase conveyance portion due to their industry proven lime injection airlock volumetric rate control. Their system is designed to eliminate plugging by maintaining flow rates through an airlock rate control, which is not affected by changes in material sizing. Coperion has operational equipment in many steel plants, including carbon injection systems, that go alongside lime injection systems.
Tallman Technologies brings design and engineering expertise in supersonic lime injection technologies. Their patented lime injectors are some of the most efficient on the market and not only reduces the loss of lime to off-gassing but also improves customer sustainability goals by significantly reducing scope 2 and 3 CO2 emissions.
Carmeuse Systems combines all this experience to offer steelmakers one of the most effective lime injection systems in the market. To take it a step further, at our test facility, we can configure it to simulate your system parameters, run your supplied lime and establish site-specific settings. This ensures smooth startup and operation, along with optimizing settings based on the characteristics of your lime supply and system configuration.
That is the Carmeuse Systems difference!
Documents and Brochures
Related Blogs